AMDEC inversée / Reverse FMEA : Un outil pragmatique pour robustifier vos process de fabrication
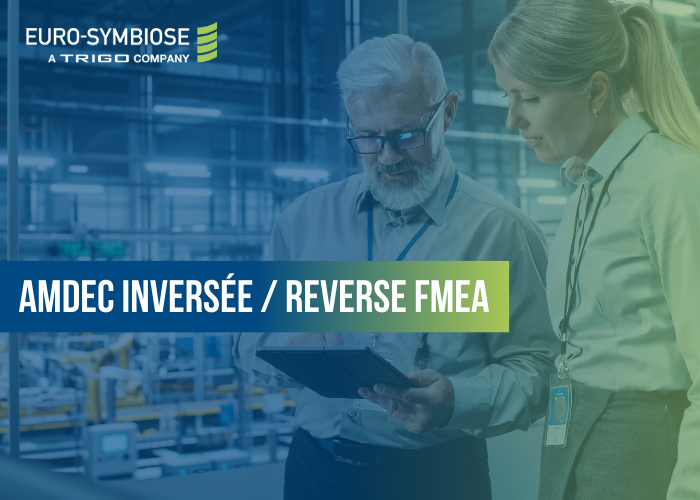
De plus en plus de constructeurs automobiles, tels que STELLANTIS, RENAULT, FORD, GM, et des fournisseurs de rang 1 exigent la mise en œuvre de l’AMDEC inversée en vie série. En quoi consiste cette méthode et quels bénéfices concrets peut-elle apporter à mon entreprise ?
L’AMDEC inversée est une démarche terrain qui vient compléter les outils d’analyse de risque, principalement l’AMDEC Process, et potentiellement l’AMDEC Moyen. Cet outil très pragmatique se focalise sur la vérification de l’efficacité des mesures prises pour maitriser les process de fabrication et la qualité des produits, en venant confronter la réalité à la théorie de l’Analyse des Modes de Défaillances, de leurs Effets et de leur Criticité.
L’AMDEC inversée est un outil d’amélioration continue permettant à la fois de vérifier la robustesse des process de fabrication en fonctionnement, tout en prenant en compte les retours d’expérience, pour faire évoluer les AMDEC Process – génériques et spécifiques – des installations actuelles et futures.
Les principaux objectifs de l’AMDEC Inversée :
L’AMDEC Inversée permet de vérifier concrètement que toutes les actions de prévention et de détection, définies lors de l’analyse AMDEC Process, faite en phase projet, sont effectivement bien mises en œuvre, efficaces et pertinentes sur les process de fabrication en fonctionnement. L’AMDEC inversée permet également de s’assurer que les hypothèses formulées initialement ont bien été évaluées et permettent réellement de réduire les risques identifiés. Ceci permet potentiellement de découvrir de nouveaux modes de défaillance pouvant engendrer des risques non identifiés initialement. A noter que l’AMDEC Process initiale se veut la plus exhaustive possible sur les points les plus à risques, mais il est parfois difficile de considérer toutes les sources de défaillance et leurs causes, par manque de retours d’expérience ou par manque de ressources.
L’objectif de ces vérifications est de faire évoluer l’AMDEC Process, afin d’en faire un outil d’amélioration « vivant ». Cela permet également aux entreprises de se réconcilier avec la pratique AMDEC Process, en créant une dynamique de mise à jour des AMDEC Process génériques et spécifiques, en cohérence avec la réalité du terrain, en retrouvant une valeur ajoutée à la méthodologie AMDEC Process, et ainsi avoir une meilleure maîtrise des risques pour in fine obtenir des résultats tangibles de baisse des taux de rebuts internes et de réclamations clients.
La mise en œuvre de l’AMDEC inversée :
L’AMDEC inversée s’effectue dans l’atelier, au pied des machines et des installations. Ce tour d’atelier se focalise sur les points critiques et se fait en équipe pluridisciplinaire (production, industrialisation, maintenance, qualité…), afin que chaque service concerné puisse partager les constats d’efficacité des mesures définies au préalable, lors du développement process, ou bien lors d’une AMDEC inversée précédente.
La phase de préparation :
La phase de préparation qui consiste à identifier les priorités pour l’analyse terrain, en collectant les données d’entrée spécifiques au process (spécifications produits, caractéristiques sécurité, réglementaires, critiques, synoptique de fabrication, plan de surveillance, indicateur qualité de production, réclamations client…) et en investiguant dans l’AMDEC Process pour venir sélectionner plusieurs lignes de l’analyse, suivant certains critères (indice de gravité, l’indice de RPN ou AP), qui feront l’objet de vérifications sur le terrain.
La phase d’analyse terrain dans l’atelier :
La deuxième phase est l’analyse terrain à proprement parler qui consiste à observer la bonne mise en pratique des mesures prévues, à échanger avec les opérateurs, superviseurs, techniciens qualité et de maintenance qui connaissent les dérives et dysfonctionnements existants, mais qui ne sont pas systématiquement remontés ou bien traités. Cette phase d’observation sur le terrain est le bon moment pour observer le déroulement des opérations de fabrication, de manipulation, de stockage et d’imaginer des modes de défaillance qui n’auraient pas été identifiées pendant la première analyse AMDEC Process.
Il y a également la pratique qui consiste à simuler de nouveaux modes de défaillance, tels que des absences de pièces, des mauvais positionnements de pièces, des mauvais dosages de matière… et vérifier si le procédé de fabrication empêche la création de défauts ou permet de les détecter sur le poste ou à une étape ultérieure. Il faut mener ces activités de simulation avec précaution pour ne pas endommager les outils de production, ou ne pas détériorer le produit, qu’il serait difficile de récupérer dans le flux des produits en-cours.
À l’issue de cette phase d’analyse terrain il faudra, en fonction des constats et risques identifiés, définir potentiellement des actions de sécurisation immédiates pour protéger vos clients des nouveaux risques identifiés, avant de les traiter avec des actions correctives.
Donnée de sortie de l’AMDEC inversée :
La troisième phase est la donnée de sortie de la démarche, qui consiste à mettre à jour l’AMDEC Process à partir de vos observations, en intégrant tous les nouveaux modes de défaillances et causes découverts. Il s’agira également de réviser les cotations d’occurrence et de détection sur la base des données de performance en vie série, ce qui peut amener à déclencher de nouvelles actions de maitrise des risques. La mise à jour de l’AMDEC Process déclenchera potentiellement la mise à jour de tous les documents associés, plan de surveillance, instructions de travail, plan de maintenance… .
Comme expliqué, cette méthodologie est pragmatique et très concrète. Elle permet de mettre en phase l’identification des risques, les actions correctives et la documentation avec la réalité du terrain.
Planification de l’AMDEC inversée :
Les clients demandent la mise en place d’une planification de ces activités, qui doit rester flexible en fonction d’éléments déclencheurs tels que le démarrage d’un nouveau process de fabrication, des modifications produit ou process, des réclamations client ou des taux de rebuts élevés.
Aucune fréquence n’est imposée par les clients mais l’idée implicite est d’en faire un outil dynamique de révision des AMDEC Process. Il est donc recommandé de prévoir des durées courtes mais avec des fréquences régulières, (par exemple une séance de 2 à 3 heures par mois), plutôt qu’une révision annuelle comme cela peut être pratiqué pour de nombreux outils qualité.
Pour en savoir plus et pratiquer ensemble, EURO-SYMBIOSE propose deux modules de formation : un premier module d’une journée, en présentiel ou à distance, pour découvrir la démarche et pratiquer sur un cas d’étude standard. Un deuxième module de 2 jours, en présentiel sur votre site, en appliquant l’ensemble des phases de la méthode dans votre contexte, vos ateliers, jusqu’à la mise à jour de vos AMDEC. Vous pourrez ainsi démontrer à vos clients que vous maitrisez la méthodologie et que vous en faites un outil d’amélioration continue.
Pour aller plus loin
Retrouvez ci-dessous les formations EURO-SYMBIOSE dédiées à l’Amdec Process Inversée / Reverse FMEA :