Infos
Conseils pour un 8D efficace
- 24 avril 2019
- Publié par : Maélise ROBERT
- Catégorie : Aéronautique Automobile
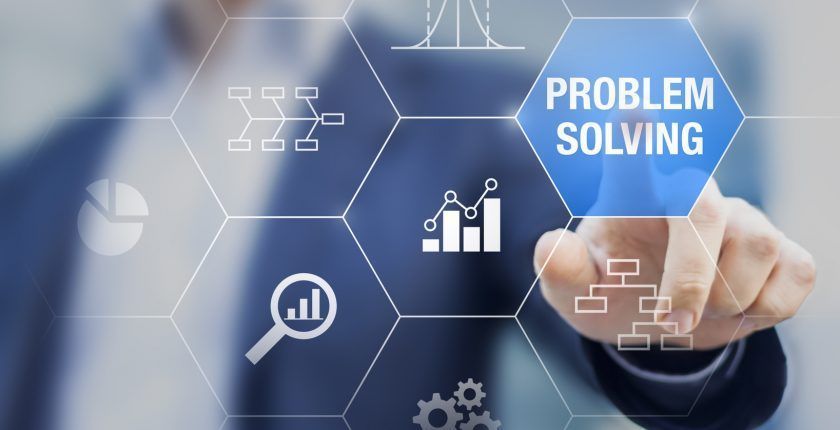
Rédaction : Bertrand HEINRICH, Directeur Général d’EURO-SYMBIOSE.
La méthode de résolution de problèmes 8D, abréviation de 8 Disciplines, a été mise en place par FORD en 1987. Elle vise à systématiser l’utilisation d’une méthode structurée, participative et transversale pour résoudre efficacement un problème qualité.
Rappelons tout d’abord que les objectifs d’un 8D sont de protéger le client et éviter la récurrence.
Un 8D efficace passe nécessairement par :
- La constitution d’une équipe pluridisciplinaire qui traitera le problème.
- La description du problème à travers l’utilisation du QQOQCCP et du Est/N’est pas afin de limiter le champ des investigations et identifier rapidement des pistes plausibles à explorer.
- Un suivi quotidien des défauts par date de fabrication et par lieu de détection avec l’objectif à atteindre pour vérifier graphiquement l’efficacité des mesures de protection et des actions correctives.
- Des mesures de protection immédiates du client pour l’ensemble des produits à risque, quel que soit leur état d’avancement dans le processus de fabrication, couvrant tous les points de stockage et de livraison.
- Une analyse de causes avec le 5 Pourquoi (5P) qui permet d’identifier les causes racines techniques et de remonter aux causes organisationnelles et managériales.
- Des actions correctives qui portent sur l’ensemble des causes identifiées.
- La levée des mesures de protection du client après avoir démontré l’efficacité des actions correctives.
- La reconnaissance du travail accompli et le partage des connaissances dans toute l’organisation.
- La capitalisation et transversalisation des actions correctives sur les produits et processus similaires : mise à jour des AMDEC et des plans de surveillance, création ou mise à jour des standards de conception et de fabrication.
« Si j’avais une heure pour résoudre un problème, je passerais cinquante-cinq minutes à définir le problème et seulement cinq minutes à trouver la solution. » Einstein
Dans cet esprit, nous allons développer les premières étapes d’un 8D qui sont les plus cruciales pour une résolution de problème robuste.
La constitution de l’équipe
La première étape consiste à désigner le groupe de travail. La taille de ce groupe dépendra de la nature et de la complexité du problème à traiter. Un problème a des origines et des conséquences transversales, il est rarement circonscrit à un seul processus ou service : vous devez donc solliciter toutes les fonctions concernées.
Le groupe de travail sera piloté par un leader qui sera à la fois animateur, facilitateur et modérateur. Ce meneur doit être formé et aguerri à l’utilisation de la méthode 8D et aux techniques d’animation d’un groupe.
La description du problème
Outre la caractérisation classique d’un problème à l’aide du QQOQCCP, l’essence même de l’outil Est/N’est pas est de se demander non seulement pourquoi, dans certaines circonstances, le défaut apparaît, mais également pourquoi, dans d’autres circonstances, le même défaut n’apparaît pas. Et à partir de là, identifier les différences qui constituent des facteurs influents à investiguer (causes potentielles).
Il faut ensuite tracer les pièces défectueuses aussi finement que la traçabilité vous le permet : par date de fabrication, par équipe de production, par lieu de fabrication. C’est l’occasion de justifier le bien fondé des exigences relatives à la traçabilité des produits dans la clause 8.5.2.1 du standard IATF 16949. Il s’agit aussi d’être en mesure de réduire au maximum la fenêtre de production des produits à risque afin de limiter les coûts de sécurisation.
Les actions de sécurisation
L’objectif de cette étape ? Identifier toutes les pièces à risque et définir des mesures de protection immédiates.
Pour que les actions de sécurisation soient efficaces, il faut que :
- L’inventaire des lots suspects soit réalisé pour chaque emplacement de stockage : en interne, chez le client, sans oublier les pièces en transit.
- Les instructions de retouche et/ou de tri soient définies et validées par la Qualité.
- Les résultats des actions de sécurisation alimentent la description du problème (QQOQCCP, Est/N’est pas).
- Un marquage spécifique soit présent sur les pièces contrôlées / retouchées.
- Un étiquetage spécial soit présent sur les unités de conditionnement.
- Les actions de sécurisation et la traçabilité des premiers lots garantis soient communiquées au client.
- L’analyse du défaut ait démarré avec l’implication des opérateurs en production.
Des causes potentielles aux causes avérées
Cette étape est la plus complexe de toutes. Commençons par définir ce qu’est un problème : un problème c’est un écart entre une situation réelle insatisfaisante et une situation souhaitée. Les problèmes ont très souvent pour origine un non-respect de standards, une absence de standards ou des standards inadaptés.
L’équipe doit donc analyser les écarts entre la situation actuelle (pièces bonnes et mauvaises) et la situation visée (le standard) pour ensuite confirmer ou infirmer l’influence des facteurs identifiés lors de l’étape Description du problème.
Comment faire ? Par comparaison à l’aide d’un arbre des facteurs (FTA) qui permet de comprendre les conditions qui ont rendu les pièces différentes. C’est une étape clé de l’analyse. Nous ne rappellerons jamais assez que le meilleur moyen de valider une cause est de reproduire le défaut.
Pour chaque facteur validé, une analyse 5 Pourquoi (5P) doit être lancée. En effet, elle aboutit à plusieurs causes profondes qui permettent d’identifier les raisons pour lesquelles un défaut est apparu et vous a échappé. Avec les 2 premiers Pourquoi, vous traitez des causes liées au processus, c’est l’explication «technique». Le 3ème Pourquoi est essentiel pour une transition réussie entre ce qui est évident et ce qui l’est moins. Vous n’avez pas besoin de répondre aux 5P en même temps, c’est une activité d’enquête et chaque Pourquoi doit être validé avec des preuves. Lorsque vous arrivez enfin au 5ème Pourquoi, il est probable que vous ayez trouvé une cause systémique.
« Pourquoi avons-nous ce défaut maintenant ? » Si vous ne pouvez répondre clairement à cette question, il est possible que vous soyez allé trop vite ou que votre 8D soit orienté pour coller à des conclusions préconçues. Prenez du temps pour définir le problème avant de chercher la solution et justifiez bien vos conclusions avec des données.
Pour en savoir plus :